Klimafreundlich und bezahlbar: Neues Wohnhaus in Norderstedt
In Norderstedt, in Schleswig-Holstein, entsteht gerade ein Holzhochhaus, das nachhaltig und bezahlbar sein will und außerdem im Eiltempo fertig wird. Dabei wird mit viel Holz und einem neuen, zementfreien Beton gearbeitet.
Wegen seiner Beständigkeit, Druckfestigkeit und Formbarkeit ist Beton generell oft noch das Mittel der Wahl am Bau. Für die Herstellung von Beton wird allerdings Zement benötigt und dessen Produktion macht bis zu acht Prozent der globalen jährlichen CO2-Emissionen aus. Die Umweltbilanz von klassischen Betonbauten ist daher einfach schlecht - auch wenn die "Dekarbonisierung der Zementindustrie" kommt. Besonders in Skandinavien oder den Niederlanden gibt es daher schon seit längerem einen Trend zum Holzbau. Auch in Norderstedt ist ein Modellprojekt gestartet, das vieles anders machen will. Die Firma blu, ein Ableger des Hamburger Bauunternehmens August Prien, will noch dieses Jahr 71 klimaschonende Sozialwohnungen übergeben, die in einer sogenannten Hybridbauweise entstehen.
Klinker aus recycelten Steinen
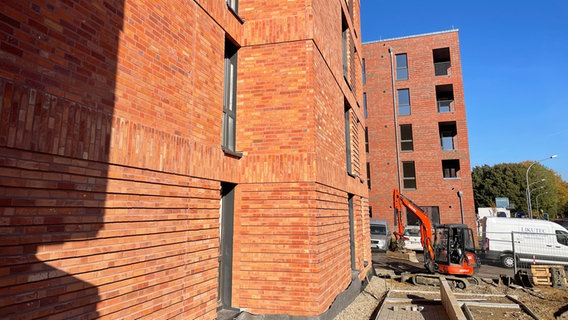
Auf der Baustelle muss man das Besondere am neuen Projekt UBS4 nicht lang suchen. Die Abkürzung leitet sich vom Straßennamen ab. Das Haus liegt an der Ulzburger Straße 168 und meint das vierte Baufeld mit drei Häusern. Dort erstrahlt eine Fassade mit rötlich-hellbraunem Klinker. Klingt gewöhnlich, ist es aber nicht. Fassade und Stein sind sehr besonders, weiß Johanna Walzel, Architektin und Planerin von UBS4: "Die Fassade ist ein vorgehängter Recyclingklinker, weil sich dahinter ein Holzbau verbirgt. Das sieht man jetzt gar nicht mehr so gut. Es war eine Vorgabe der Stadt, hier einen Klinker zu verbauen."
Wiederverwendung in Zukunft gleich mitgedacht
Johanna Walzel und Projektleiter Jens Christian Kubicki stehen vor einem fast fertigen Haus. Nachhaltigkeit ist hier eines der Hauptkriterien, wie am Beispiel des alten Klinkers aus einer polnischen Molkerei deutlich wird. Die Idee, das Ganze auf eine sogenannte Fertigteilfassade zu setzen, soll auch das Recycling in Zukunft ermöglichen, erklärt Johanna Walzel: "Wenn das Gebäude irgendwann abgerissen werden muss, könnte man es wieder in kleine Häppchen zerlegen und für ein neues Gebäude wiederverwenden. Denn alles wieder sauber machen zu müssen, ist ein Aufwand und vom Mörtel her meist gar nicht möglich."
Kombination einzelner Maßnahmen verringert CO2
Der Weg durch die Tiefgarage ins Gebäude zeigt, dass der Bau unten recht betonlastig ist. Jens Christian Kubicki weiß warum: "Letztlich ist es eine Holz-Hybrid-Bauweise: Der Keller ist zwangsläufig aus Beton, einfach aufgrund abdichtungstechnischer Maßnahmen und statisch relevanter Themen." Alles andere sei aber Holzbau als Stützen-Balken-Konstruktion. Die Außenwände seien ebenfalls als Holz. Der Beton ist ein nur für dieses Pilotprojekt zugelassener Geopolymerbeton. Der ist komplett zementfrei, und somit lassen sich bis zu 75 Prozent CO2 einsparen. Ein Schritt Richtung Nachhaltigkeit, erklärt Kubicki: "Ich denke nicht, dass jetzt alles aus Geopolymerbeton gebaut werden muss. Es sind eher die Einzelbausteine, die da wirken." Das heißt, die Gesamtkombination aus Geopolymerbeton, Holzbau und Recycling führe am Ende zu einem geringeren CO2-Fußabdruck.
Allerdings bringt die Arbeit mit Innovationen auch manchmal unvorhersehbare Schwierigkeiten mit sich. Der neue Beton härtet zum Beispiel bei Minusgraden schlecht aus. Trotzdem steht dieses Haus am Ende deutlich schneller als ein typisches Hochhaus.
Entlastung am Bau durch vorgefertigte Teile
Im Treppenhaus spiegelt sich das Tageslicht in einem verzinkten Gitterrost. Das zieht sich bis nach oben durch und bietet Sicherheit. In der Art ist es auch draußen an den Balkonen zu finden, die bündig und fast wie Regale vor der Fassade stehen und dabei materialsparend gebaut sind. Dünne Carbon-Betonplatten geben ihnen Stabilität, erklärt Johanna Walzel: "Wir können hier jedes Element wiederverwenden. Vieles davon ist vorgefertigt, wie die Fassade oder die Gitterroste. So wird der ganze Baustellenprozess massiv entlastet und beschleunigt." Das wiederum sei witterungsunabhängig und auch viel weniger fehlerabhängig, weil die Teile im Werk besser kontrolliert werden können.
Je weniger Material, desto besser
Alle Arbeitsabläufe sind optimiert - Gewerk folgt auf Gewerk. Diese Arbeitsweise kommt aus der Autoindustrie und nennt sich Lean-Taktung. Auch damit lässt sich wieder CO2 einsparen, weil der Materialtransport sich verkürzt. Bäder etwa werden als fertige Module mit Fliesen, Armaturen und Duschscheibe einfach angeschlossen. Die Küchen sind gleich und nur für Menschen im Rollstuhl etwas abweichend. Das erinnert ans Bauhaus und ein bisschen auch an DDR-Plattenbauten. Johanna Walzel zeigt eine Musterwohnung: "Hier konnten wir den Wandaufbau mit einer Strohbauplatte testen und mit den Gewerken besprechen, wie das mit den Kabeln funktioniert. Im Innenausbau wollten wir eher auf Schichten verzichten. Denn jedes Material, das ich nicht verwende, ist nun mal das nachhaltigste."
Nachhaltigkeit auf allen Ebenen
Es gibt also, neben viel Holz, weiße Zwischenwände mit Stroh, gedämmt durch nachwachsende Zellulose, gestrichen mit mineralischer Farbe. Die Räume haben einen glatt polierten Estrichboden. Im Treppenhaus trägt der Sichtbeton nur weiße Farbe - es ist auch ein minimalistisches Projekt, nordisch-schick. Auf dem Dach, das in Zukunft begrünt werden soll, stehen bald 650 Quadratmeter Photovoltaik. Geheizt wird mit Fernwärme. Trotz der vorausschauenden Bauweise ist UBS4 sozial geförderter Wohnungsbau mit Quadratmeterpreisen bis zu 8,50 Euro. Mit dem Qualitätssiegel für nachhaltige Gebäude (QNG) und dem Siegel der Deutschen Gesellschaft für nachhaltiges Bauen (DGNB) hat das Haus zwei wichtige Nachhaltigkeitszertifikate. Zudem wurde die EU-Regelung für umweltfreundliches Wirtschaften angewandt. UBS4 gilt in Schleswig-Holstein als landesweites Modellvorhaben.
17 Monate Bauzeit für ein komplettes Haus
Neben der Klimafreundlichkeit wird das Projekt auch der Forderung gerecht, besonders schnell Wohnraum zur Verfügung zu stellen. Jens Christian Kubicki erzählt vom Ablauf: "Mit dem Erdbau haben wir im August 2023 angefangen. Allerdings wurden wir ein bisschen durch die Zulassung des Geopolymerbeton ausgebremst. Ende 2024 sind wir fertig." Das liege eben auch daran, dass vieles vorgefertigt und regional produziert wurde: Der Holzbau und die Bäder etwa wurden schon vor der Baugenehmigung freigegeben.
Die Firma blu werde das Objekt ganz sicher im Bestand halten, weil sie die Konsequenzen und Risiken einschätzen könne, ergänzt Projektleiter Jens Christian Kubicki. Der Bauherr müsse auch in Zukunft wagen, neue Materialien zu verwenden. Das Risiko müsse man letztlich eingehen, um nachhaltig zu sein, sagt er.
